-
Nitin Narawade
- None
How much can automation improve CAE simulation?
<div class="text-justify"> If you didn’t already know, running simulation iterations can be quite a repetitive task, especially when the geometry changes significantly from one design to the next. Perhaps you’ve noticed how much valuable engineer and analyst time goes into the tedium of manually clicking the mouse over and over to prepare each aspect of a single model. With so much human interaction in such a fine tuned computation, there are many possible points of error, making consistent results hard to achieve. Moreover, when an experienced analyst who has minimized those points of failure with workarounds or templates decides to move on, much of his or her knowledge can be lost to the larger team. Then the slow process of generating reliable simulations begins again, often meaning that valuable product development insights don’t always reach the design or manufacturing teams in time. Reliable and intelligent automation protocol—best if easy to implement and doubles as a tool for knowledge capture—can alleviate all of these shortcomings. One question that remains is: by how much? <br/><br/>
Let’s lay out the basic steps in the traditional CAE process and take a brief look at common bottlenecks. Then we’ll try to identify, and maybe even quantify, the benefits automation can offer towards the goal of reliable and quick simulations. <br/><br/>
First, in the traditional approach, a manufacturing level CAD geometry needs to be imported and “cleaned” to be suitable for accurate simulation purposes. Creating this simulation-ready geometry is one of the more time consuming steps, requiring a lot of manual clicks to make the necessary adjustments. What if the CAD and CAE teams work in closer collaboration, so that models can be initially designed in conjunction with simulation requirements in mind? This could cut back on the significant amount of manhours currently invested in extraneous first-draft manufacturing detail, as well as the later CAD clean up. Further, if the CAE pre-processing software could directly support and integrate with different mainstream CAD platforms, then most of that tedious simulation prep work can be eliminated with automatically generated simulation-ready geometries. <br/><br/>
Next after clean up (in the traditional workflow) the simulation specialist needs to create the mesh, an array of discrete sections of the 3D model on which supercomputers number crunch through different physics analyses. Along with this step the engineer needs to manually apply all of those various physics parameters and attributes to be studied to the simulation model or mesh. These processes are the work of highly trained engineers, and require a significant level of expertise to reliably arrive at useful virtual test data. The real drag on time here is that these steps then have to be repeated for each significantly new geometry and new physics interrogation. How could an automatic process eliminate this bottleneck? <br/><br/>
Well, what if the same pre-processing software mentioned before, could hold a universal blueprint for all the physics and mesh specifications, which can be appropriately mapped to each incoming geometry and simulation model? With many fewer clicks, such a system could automatically apply the desired mesh and attributes to each incoming simulation-ready CAD model. The same highly trained engineers now put their physics expertise into the blueprint, rather than each individual geometry, and ensure that everything maps correctly from the blueprint onto the simulation models. <br/><br/>
<img src="/media/blog/blog3_1.JPG" alt="Blog image"> <br/><br/>
The beauty of this approach is that, once the process is verified, such a software system could reliably serve design or test engineers, as well as analysts for all future simulations, with only minor adjustments. And let's take it another step, just to see how a streamlined front-to-end automated simulation workflow would look like. Let’s grant our software a post-processing framework that allows for easily tailored, automatic report generation to avoid the end-process bogdown of manually creating reports, graphs, and even animations. Such an added bonus would only increase the efficiency of the whole product development cycle. <br/><br/>
So, when we eliminate the most time-intensive and non-value-adding manual aspects of traditional simulation processes, and replace them with a well structured automated workflow enabled by dedicated software, how much would an organization improve their own product development cycles? While it can be hard to quantify, as each organization will be different, there is evidence of such systems in place granting anywhere from a 3-7x increase in process efficiency. On average, CAENexus customers were able to improve their workflow efficiency by over 500% with the use of their pre-processing software package, which provides all of the benefits described above. If you’d like to see just how much your organization could improve, contact Novus Nexus at <span class="blue-text">info@novusnexus.com.</span> <br/><br/>
Nitin Narawade <br>
Business Development Lead, Novus Nexus <br>
Simulate better with <span class="blue-text">us</span>.<br>
<a href =https://www.novusnexus.com >www.novusnexus.com</a></div>
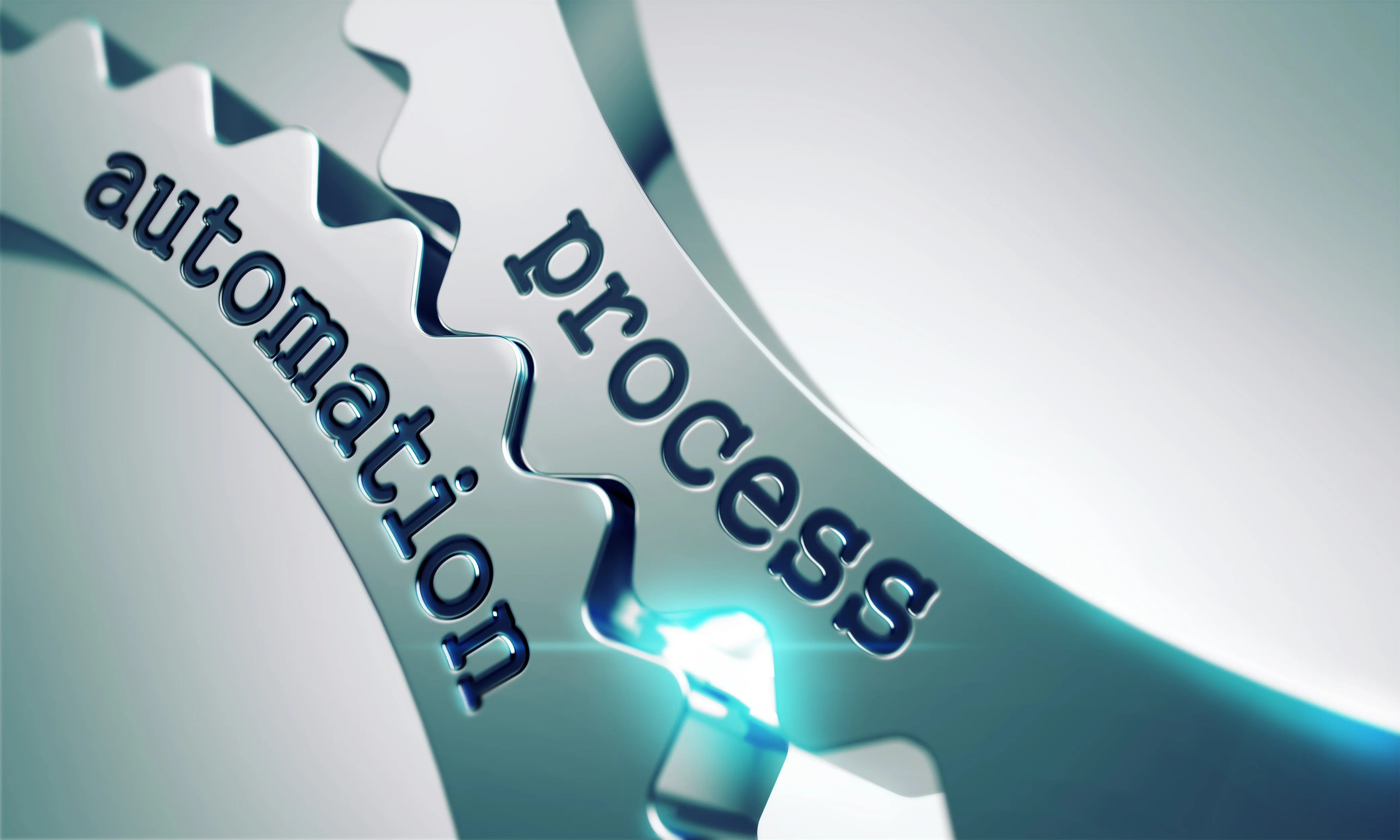